
Full Head Casting
Health and Safety
- Constantly talk to your model
- Look out for any nervous ticks and try and reassure them
- Don't mess about or try and make model laugh
- DON'T use straws
- Do not do it if your model has any kind of flu/cold/cough etc
- The model is the most important person in the room
- Model can still hear - maybe have a radio on to relax the atmosphere
- Apply a bald cap. You can use cap plastic and blend the edges or you can use latex and have an obvious edge - it doesn't matter (if you don't want ears in your mould then cover the model's with the bald cap and mark them when you draw in the hairline).
- Tape a bin bag to around your model
- Vaseline can work as a release on the model, but Nivea hand cream works better. If you use to much vaseline then the plaster can slide off, too much Nivea will not do this. Apply it to the skin.
- Draw on model's hairline with makeup that ISN'T GREASEBASED. Snazaroo works fine
- Have all the plaster, buckets etc all set up
- Experienced casters only need 2 people. For a first time, have about 4 people
- Make sure model is in a good, comfortable upright position. Make sure they keep their head level and chin up
- Research methods for how different people do different lifecasts (Neil Gorton's DVD)
- Lets tutors know if you are doing one so they can check on your first one
Method
- Double fold plaster bandage and apply on the back side of the head and shoulders. Find the central line along the head and shoulders. Behind the ears. Outline where you're going to go and then fill in. (YOU CAN DO THE WHOLE THING IN ALGINATE/SILICONE, but because the back is totally lacking in details and just shapes, it can be done just in plaster). Have folded edge of plaster at the front, along the line.
- After first layer, repeat. 3 layers. Then do rope layers around the edge to strengthen the mould when pulling it apart. A coupe of pieces coming down the back (sticking out from the rest) for more support.
- Make a few ropes and lay it from top to bottom and around the circumference. Then cover them with normal bandage again.
- Tap to see if its dry
- Alginate won't stick to itself once its set. Bicarbonate of soda in water - paste it on surface of layer of alginate and it will stick to itself again.
- Around 2 bags of alginate
- Add Nivea over any facial hair and the bald cap, as alginate will stick to the bald cap, and to edge of plaster
(no minty or fibrous alginate)
- Cover face in alginate
- DON'T PANIC
- After alginate has set, scrape off the overlapping excess alginate from the plaster so they both lie flat and pull of any large excess bits to neaten and for weight
- Cover plaster with Nivea - A LOT
- Start plastering over the alginate, work around the ear
- Make an obvious seam join between the two plasters
- Add ropes and plaster over that
- Before you de-mould, draw some line-up lines accross the seamlines to make sure the mould matches up (sharpie or snazaroo)
- Have model keep eyes closed and model stay still. Turn lights off as to not shock the model. Sometimes the back falls off first, sometimes the front....
- Use finger to help release ears
- Then prepare it for filling......
- Superglue alginate and plaster around the nose area. Superglue will react with water and will go rock-solid
- Then mix some really thick alginate so that it can be pushed through the nostrils and create nostrils when material is poured in. Cover the nose and then cover that with plaster
- Then put halves together, line-up registration points and look for edge
- Then plaster two halves together. Leave some raggedy edges so you can see where to pull it apart for later.
- You need to process it straight away. If its being left for an hour or so, cover with wet paper towels, but it should be filled straight away as the alginate will start to shrink
- NIVEA ALL OF PLASTER SIDE BEFORE FILLING
- DON'T fill it with solid plaster, as the heat generated will heat it and cause it to crack
- Pour half in and smooth it round the sides, thicken it and mix it up the sides, use some matting up the sides and then leave overnight to set
![]() image5.jpeg | ![]() image6.jpeg | ![]() image7.jpeg | ![]() image8.jpeg |
---|---|---|---|
![]() image9.jpeg | ![]() image10.jpeg |
Brick In The Yard Mold Supply (2012) [online] Moldmaking and Casting: 2 piece hydrocal head mold. Available from:https://www.youtube.com/watch?v=M38Z0A_hw20&spfreload=10 [Accessed: April 6th 2015]
Notes:
- the kind of mould you would use to make gel 10 positives or flexible foam positives
- start by usin a tex-clay positive pulled from an alginate head cast. Tex-clay is backed up with plaster and hydrocal in shoulders
- hydrocal is just in shoulders as if it was in the head it could cause problems with undercuts
- lay head on the back and build up wall around it with scrap pieces of wood. Then build up wall in water-based clay. Work quick so the clay doesn't dry out and crack. (spray water bottle). CLay should stick out at a 90 degree angle.
- scrape off and flatten surface. eliminate all undercuts. Go under ears. Also cut around edge to be clean outside edge
- Add keys. Make sure there is no clay on the sculpture
- Paint on hydrocal. Mix with 1 cohesive batch. 3 stages of drying; liquid, then paste, then putty.
- When hydrocal is slightly thicker, you can add fiberglass and layer it up. Burlap or hemp fibre could also be used. Fibreglass keeps mould thinner
- Hemp is stronger but more expensive
- Fibreglass matt allows the hydrocal to penetrate it
- Don't press to hard as you don't want it to go through to the head
- overlap. Don't skip on reinforcement near the edge
- Add hydrocal over the fibreglass at the end. Should be about an inch/inch and a half thick overall. Can wet your hands and smooth down as much as possible
- (can polish the mould with hemp)
- After sitting for about an hour, the wall can be pulled away and the second half of the mould cab be made.
- Cut away any excess plaster from the flange
- Then apply paste wax as a mould release (don't need any on the tex-clay positive) on the exposed plaster edge. 15 minutes drying time
- Then repeat exact same process on second half
- Clean out mould with naptha.
![]() Screen Shot 2015-04-07 at 14.16.44.png | ![]() Screen Shot 2015-04-07 at 14.18.20.png | ![]() Screen Shot 2015-04-07 at 14.20.46.png | ![]() Screen Shot 2015-04-07 at 14.21.26.png |
---|---|---|---|
![]() Screen Shot 2015-04-07 at 14.21.42.png | ![]() Screen Shot 2015-04-07 at 14.21.52.png | ![]() Screen Shot 2015-04-07 at 14.22.10.png | ![]() Screen Shot 2015-04-07 at 14.22.56.png |
![]() Screen Shot 2015-04-07 at 14.24.10.png | ![]() Screen Shot 2015-04-07 at 14.25.01.png | ![]() Screen Shot 2015-04-07 at 14.25.55.png | ![]() Screen Shot 2015-04-07 at 14.26.06.png |
![]() Screen Shot 2015-04-07 at 14.26.50.png | ![]() Screen Shot 2015-04-07 at 14.27.19.png | ![]() Screen Shot 2015-04-07 at 14.36.57.png | ![]() Screen Shot 2015-04-07 at 14.38.53.png |
![]() Screen Shot 2015-04-07 at 14.39.49.png | ![]() Screen Shot 2015-04-07 at 14.40.12.png | ![]() Screen Shot 2015-04-07 at 14.42.33.png | ![]() Screen Shot 2015-04-07 at 14.43.03.png |
![]() Screen Shot 2015-04-07 at 14.43.48.png |
Further Research; other materials and techniques
Brick In The Yard Mold Supply (2013) [online] Lifecasting: Gel-10 Headcast. Available from:https://www.youtube.com/watch?v=7GHvuqDHpec&spfreload=10 [Accessed: April 6th 2015]
Notes:
-
Paint 2 layers of platsil gel10 in a 1:1 ratio on a red head. Wait 15minutes for the first layer to dry and then after the 2nd coat wait 40 minutes. Can pigment it…..
-
Talc and remove
-
Apply the cap to the model using more platsil gel 10. This is because the bald cap will become part of the head cast, so don’t use spirit gum or telesis
-
Release skin with nivea
-
5 minutes of working time for first detail coat
-
Then a tinthicks thickener (polyfibres) for second layer.
-
Minimum thickness is a quater of an inch
-
Then plaster over the front half, vaseline it and then do the back half
-
To remove, pull off back half of plaster, then cut up the back of the silicone using you fingers as a barrier
-
Fill nose with some silicone
-
Can then fill and cast with any kind of gypsum products, monster clay, easy flow 120 casting resin to slosh around and make a hollow positive
I think if i'd needed a full headcast, I would've used this method. It seems to be quick, effective and then you can fibreglass straight into it.
![]() Screen Shot 2015-04-07 at 14.53.14.png | ![]() Screen Shot 2015-04-07 at 14.53.29.png | ![]() Screen Shot 2015-04-07 at 15.00.15.png | ![]() Screen Shot 2015-04-07 at 15.01.50.png |
---|---|---|---|
![]() Screen Shot 2015-04-07 at 15.03.12.png | ![]() Screen Shot 2015-04-07 at 15.03.56.png | ![]() Screen Shot 2015-04-07 at 15.07.17.png | ![]() Screen Shot 2015-04-07 at 15.14.02.png |
![]() Screen Shot 2015-04-07 at 15.14.16.png | ![]() Screen Shot 2015-04-07 at 15.14.21.png | ![]() Screen Shot 2015-04-07 at 15.14.28.png |
This video illustrates a very similar method to the one we were taught in class, but using silicone instead of alginate as the casting material, which can pick up more detail.
The clever part of the method which i've never heard of before, is making a silicone bald cap which will then come off and become part of the head cast. Other than that, the process is virtually the same. Obviously silicone is more expensive, but it does pick up more detail and will not shrivel and dry out like alginate.
Full Body Lifecast
Notes:
- about £500 worth of silicone
- done on a large piece of drywall. Rub Mylar into the surface so that the silicone doesn't stick to the drywall
- Cover model in vaseline
- 1st layer of straigh A and B gel10. No Deadener - this makes it slightly harder to move it around (5 minutes working time)
- Spread the silicone out and around a little so that it creates a flange for the mould. This will make it easier to seperate from the plaster mother mould
- thicken the second layer with polyfibre
- ALso add tinthicks to the 3rd layer
- Fill in the gap layers so the plaster bandage emoval is easier.
- You want about a quarter of an inch thickness. Try and make it as smooth as possible
- can also spread out soapy water with your hands on the silicone
- then apply bandages. The heat from the plaster bandage will help accelerate the drying time of the silicone
- never include a head in the full body cast, as your model wouldn't be able to communicate - its v dangerous. Do it seperately.
- can use a vacuum to clean any excess plaster or materials out of the mould
- trim the silicone edge to that its neat
- Then start painting in the melted texclay or monster clay
- don't let the clay exceed boiling point, as all kinds of problems can be caused
- In some areas where you want to build up the clay to be thick, let it cool in the crockpot for a while so its thicker and then paint it on
- Build clay up to about half an inch
- Then paint in rigid expanding foam. Don't try and fill the mould with one batch. You don't want to foam to 'mushroom' over the edge of the clay
- Attatch clay head to vlay body (take measurements beforehand to help allign)
Brick In The Yard Mold Supply (2013) Lifecasting Tutorial: Gel-10 Body Mold Part 1. [online] Available from:https://www.youtube.com/watch?v=nDPc8ckbCq0&spfreload=10 [Accessed: April 12th 2015]
Brick In The Yard Mold Supply (2013) Lifecasting Tutorial: Gel-10 Body Mold Part 2. [online] Available from:https://www.youtube.com/watch?annotation_id=annotation_1455225451&feature=iv&src_vid=nDPc8ckbCq0&v=FSCB0nh1RJE [Accessed: April 12th 2015]
![]() Screen Shot 2015-04-12 at 09.55.04.png |
---|
![]() Screen Shot 2015-04-12 at 09.55.52.png |
![]() Screen Shot 2015-04-12 at 09.56.20.png |
![]() Screen Shot 2015-04-12 at 09.58.43.png |
![]() Screen Shot 2015-04-12 at 10.02.02.png |
![]() Screen Shot 2015-04-12 at 10.05.55.png |
![]() Screen Shot 2015-04-12 at 10.06.44.png |
![]() Screen Shot 2015-04-12 at 10.08.01.png |
![]() Screen Shot 2015-04-12 at 10.11.31.png |
![]() Screen Shot 2015-04-12 at 10.12.32.png |
![]() Screen Shot 2015-04-12 at 10.18.07.png |
![]() Screen Shot 2015-04-12 at 10.19.35.png |
![]() Screen Shot 2015-04-12 at 10.22.58.png |
![]() Screen Shot 2015-04-12 at 10.24.50.png |
![]() Screen Shot 2015-04-12 at 10.28.57.png |
![]() Screen Shot 2015-04-12 at 10.31.30.png |
![]() image5.jpeg | ![]() image6.jpeg |
---|---|
![]() image7.jpeg | ![]() image8.jpeg |
![]() image9.jpeg |
M Spatola The Monstrous Makeup Manual Book Number 2 (2010) London: uknown


Tokyo SFX Makeup Workshop A Complete Guide to Special Effects Makeup (2012) London: Titan Books
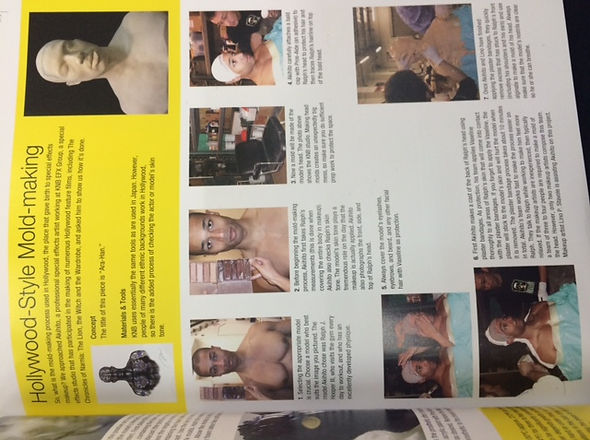
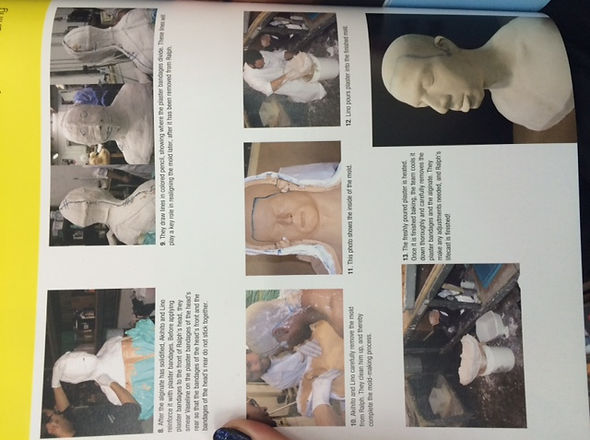
Tokyo SFX Makeup Workshop A Complete Guide to Special Effects Makeup (2012) London: Titan Books
This book shows a very similar method to the silicone head casting video. It goes on to say that you can fill the silicone with ultracal, urathanes and fibreglass and have multiple copies in different materials.
It also says that if you just need to create a plaster head then use alginate to save on money.

Benam (2015) Body Double Skin-Safe Silicone [online] Available from:http://www.benam.co.uk/products/lifecasting/body-double/ [Accessed: April 26th 2015]
This is the product used in the book, which appears to be like most other life-casting silicones, for example PS Composite's Go Cast.
If you want to produce a fibreglass core of your model there are 2 main different methods.
1. Silicone headcast your model the same way you would with alginate and plaster. Fibreglass into the two halves seperately and then join them together. I have tried to find research for this method but can't find any
2. Alginate head cast your model and make a plaster positive. Then silicone mould this and then you can fibreglass into the silicone mould.
© 2023 by Tennis Lessons with Karen. Proudly created with Wix.com