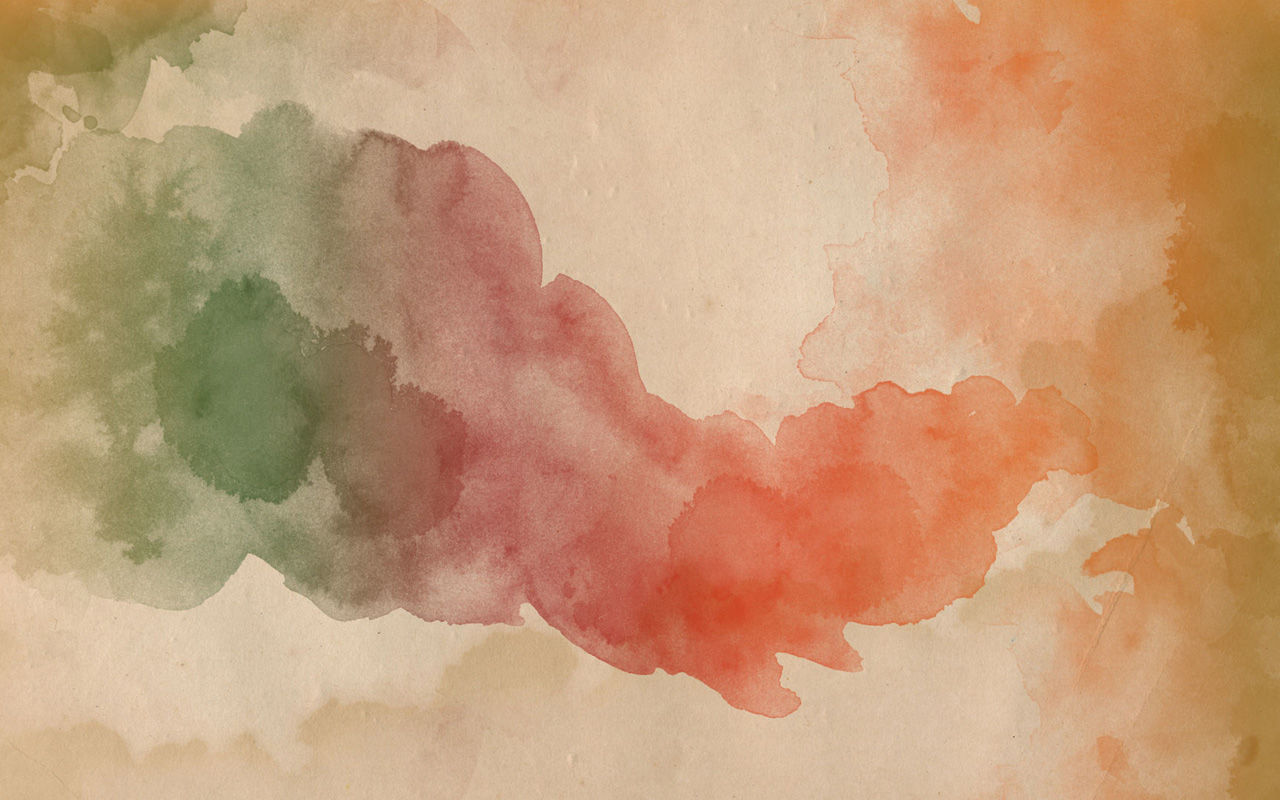
Claire Golby
Level 5
Dramatic Contexts
Arts and Technology, using their equipment. Equipment for a pilot program has since been constructed at the Ontario Crippled Children's Centre. The equipment consists of:
-
A frame on which the plastic sheet is clamped
-
An infrared heated oven (7000 watts)
-
Guides for sliding the heated plastic to a position over a vacuum table
-
A vacuum table or platen on which the cast is placed. The table can be raised by compressed air to contact the underside of the frame
-
A vacuum source with a control valve-the source is a vacuum pump and a large metal tank
The equipment can be used for sheets of an 18" x 12" size. This size is ideal for forming small orthotic items, such as ankle splints, on a production basis and for experimenting with different plastics and processes. The 18" x 12" size can be adapted easily to form 12" x 12" circular sheets for the production of polycarbonate sockets. A great deal of operator skill is required to form the sockets shown in Fig. 6which are 10 ½ in. deep and exhibit a draw ratio of (3 ½):1, which is an extremely high ratio for polycarbonate. The clear sockets will be evaluated by patient fittings and wear. To date only a few have been fitted ( Fig. 7 ). The vacuum forming of deep sockets requires further development and research in order to achieve a technique with a suitable reliability factor. Clear polycarbonate sockets seem to have a very promising future. Some of the items in service so far, produced by this process at the George Brown School and OCCC.
Some of the materials which lend themselves to vacuum forming are:
Polycarbonate ; trade name, Lexan . A tough, rigid, transparent, thermoplastic which has useful engineering applications, e.g., gears and structural members. It has excellent dimensional stability and very low creep under load, is self-extinguishing: has fair chemical resistance, excellent impact resistance, and draws well (2:1 ratio). Lexan is one of the most promising plastics: it has already been used for clear back panels in orthotics and clear sockets in prosthetics. Compared with other plastics. Lexan is relatively expensive but its versatility more than compensates for this drawback. A minor disadvantage is that the sheet to be formed must be pre-dried several hours before vacuum forming.
Acrylonitrile Butadiene-Styrene - A.B.S. Is very tough, with an unusual combination of high rigidity and impact resistance: has excellent thermoforming properties and a high drawing ratio (4:1) with maintenance of a uniform wall thickness. It has fair chemical resistance; very low moisture absorption; good dimensional stability, and high abrasion and heal resistance. Its excellent thermal properties allow A.B.S. to be hand moulded, in the same manner as San Splint, only at slightly higher temperatures, to produce a structure that is much stronger than most other hand-moulded materials. A distinct disadvantage of A.B.S. is that it is not available in transparent form. A Japanese firm will soon be supplying a form of A.B.S., designated as M.B.S. which will be available in Canada. This new material exhibits all the desirable properties of A.B.S. plus the fact that it is transparent.
Polyethylene -High-Density. Has a good combination of physical strengths; tensile, flexural and impact. Fabrication techniques are simple and the material cost is low. It is easily heat-sealed but heat resistance is limited to 180 deg. Polyethylene has exceptional chemical resistance; however, it does have high shrinkage and cold flow under load. It has a fair drawing ratio (2.5:1). Because of its very low cost it is a good material for trial fittings and the production of many items where transparency is not necessary. Polyethylene has a natural lubricating or stick-free surface which exhibits a very low coefficient of friction.
Polypropylene . Has excellent resistance to stress fatigue, and is widely known for "living-hinge" applications. Has a low specific gravity; excellent impact strength, with a scratch-resistant surface; and good chemical and heat resistance up to 240 deg. It is translucent, allowing visual appraisal of contact fit. The draw ratio is limited to 1.5:1. It is difficult to form over a wet cast without a suitable moisture barrier. It is in the same chemical class as polyethylene (Poly-olefin) and consequently it is relatively inexpensive. Since the temperature range for forming is narrow, it is difficult to heat polypropylene to vacuum-forming temperatures without creating built-in stresses. Special care must be exercised to prevent these stresses.
Cellulose Acetate Butyrate-C.A.B. A tough, clear plastic suitable for thermoforming (3:1 ratio). It is primarily used as a cheap replacement for Lexan where strength is not important. It has poor solvent resistance and shatters under severe bending. Because of its low cost and transparency, it is useful for experimental testing of vacuum-forming techniques.
Artamonov, A. (2014) Vacuum-Forming Techniques and Materials in Prosthetics and Orthotics. The Association of Children's Prosthetic Orthotic Clinics. [online[ Available from:Vacuum-Forming Techniques and Materials in Prosthetics and Orthotics [Accessed: December 10th 2014]

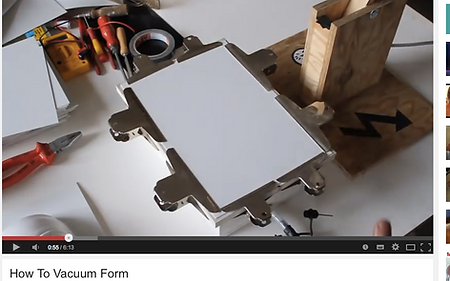
Vacuum Forming
Vacuum forming, while thought by many to be a relatively new method of fabricating plastic materials, is actually one of the oldest. The process has a history dating well back into the 19th century, although the techniques involved have been changed by modern technology and materials.
The process consists of heating a thermoplastic sheet to its softening temperature, and forcing the hot and flexible material against the contours of a mould by mechanical, air, or vacuum pressure. When held to the shape of the mould and allowed to cool, the plastic retains the shape of the mould. Cutting and trimming plastics can be done with a band or Stryker saw and standard wood sanding methods. Solvents can be used to provide smooth edges quickly. Plastics can be bonded mechanically with bolts or rivets, or, in some cases, chemically to produce strong efficient joints.
The initial experiments of this Centre in vacuum forming orthotic devices were carried out in cooperation with the George Brown School of Applied
Aram Bartholl. (2012) How to Vacuum Form. [online] Available from;https://www.youtube.com/watch?v=eE26y-r63vY [Accessed: December 10th 2014]